§ 1 Древесные пиломатериалы
и фанера.
Малые суда, проекты, которых помещены в этой книге, могут быть
построены из дерева, фанеры, стеклопластика и металла. Однако
и сегодня наиболее доступным для судостроителя-любителя вариантом
остается древесина-легкий, достаточно прочный и легко обрабатываемый
материал. Возможность использовать при постройке синтетические
водостойкие клеи и фанеру позволяет конструктору и строителю по-новому
использовать этот древний судостроительный материал.
Из всего многообразия пород древесины, распространенных в нашей
стране, для постройки корпусов судов могут использоваться не более
десятка-отличающиеся влагостойкостью и прочностью.
Для изготовления наружной обшивки пригодны хвойные породы, содержащие
в своих волокнах смолу, и дуб, в древесине которого имеются дубильные
вещества, препятствующие загниванию. Из ясеня можно делать шпангоуты
и набор. Другие породы в судостроении можно применить только для
деталей внутренней обстройки и то после принятия специальных мер
для защиты их от загнивания. Бук на малом судне лучше не применять,
так как в условиях повышенной влажности он быстро загнивает и
"задыхается" без доступа воздуха, если его защитить водостойкими
покрытиями.
Наибольшее применение в малом судостроении получили сосна, ель,
лиственница, кедр, дуб и ясень, а из импортируемых в СССР пород
- красное дерево различных разновидностей и гондурасский кедр.
Сосна имеет высокую прочность, легка (объемный вес 0,51-0,55
т/м3), прямослойна, легко обрабатывается. Применяется для всех
деталей набора и наружной обшивки. Следует предпочитать мелкостройную
сосну желтоватого оттенка.
Ель-менее прочна, легко колется, но обладает хорошей
водостойкостью. Считается хорошим материалом для наружной обшивки,
шпангоутов, продольного набора. Объемный вес - 0,46 т/м3.
Лиственница обладает твердой прочной древесиной, с прямыми
мелкими слоями. Объемный вес-0,66 т/м3. Доски из лиственницы не
коробятся в такой степени, как из ели или сосны, но легко раскалываются
и дают трещины при переменном воздействии воды и солнца. Для обшивки
малых судов ее лучше не применять.
Сибирский кедр - легкая (объемный вес 0,44 т/м3), плотная
мягкая порода древесины; хорошо обрабатывается. Пригоден для обшивки
и деталей набора, Дуб-очень прочная и твердая древесина, не только
хорошо сохранявшаяся в воде, но и не теряющая в ней упругости.
Дуб применяется для изготовления деталей набора корпуса;
он является незаменимым материалом для изготовления форштевней,
киля, скуловых стрингеров, наиболее нагруженных шпангоутов, хотя
обработка дуба сравнительно трудоемка. Объемный вес-0,72 т/м3.
В отличие от хвойных пород, прочность дуба тем выше, чем шире
годичные cлои, так как В широких слоях преобладает более плотная
и твердая летняя древесина.
Древесина ясеня также обладает твердостью и упругостью
и, кроме того, сравнительно легко обрабатывается. Объемный вес-0,66
т/м3. Употребляется ясень для изготовления гнутых шпангоутов,
бимсов, круглых и овальных комингсов. В ясене хорошо держится
крепежный материал-гвозди и шурупы. Если, например, для ели сопротивление
выдергиванию забитых гвоздей принять за 1,0, то у сосны оно будет
1,7, у дуба-2,1, у ясеня-2,5. Следует отметить, что при плохой
вентиляции помещений судна ясень быстро теряет свои качества,
а дубильная кислота, содержащаяся в дубе и ели, способствует интенсивному
разрушению незащищенного стального крепежа.
Если какая-либо деталь набора, предусмотренная в проекте из сосны,
изготовляется из дуба или ясеня, площадь ее поперечного сечения
можно уменьшить на 10%.
Из пород красного дерева в судостроении наиболее часто используют
махагони. Эта древесина имеет красивую текстуру коричневато-красного
или коричневого цвета; она плотная, твердая и тяжелая (объемный
вес-0,54- - 0,75 т/м3). Красное дерево отличается малым поглощением
влаги, высокой стойкостью против гниения, мало коробится и очень
редко трескается. Эта порода широко применяется для наружной обшивки,
переборок и отделки внутренних помещений катеров и яхт высшего
качества.
Гондурасский кедр имеет мягкую древесину красноватого
цвета с объемным весом 0,5-0,65 т/м3, легко обрабатывается. Применяется
для обшивки легких гоночных лодок и яхт. Легко впитывает влагу,
поэтому чаще всего кедровую наружную обшивку защищают несколькими
слоями водостойкого лака.
Береза в малом судостроении используется, главным образом,
в виде фанеры или шпона (узкие тонкие полосы, из которых выклеивают
скорлупную обшивку небольших шлюпок и катеров).
Древесина как судостроительный материал обладает и рядом отрицательных
свойств, которые следует учитывать при постройке корпусов.
Влажность - содержание влаги в древесине в процентном
от ошении к ее массе - определяет не только основные технологические
свойства материала, но и устойчивость формы готовых конструкций,
и их прочность. При постройке судов применяют древесину с содержанием
влаги от 12 до 18 %. Более сухой материал не рекомендуется, так
как при набухании древесины в готовой конструкции ее линейные
размеры увеличиваются, появляются большие нагрузки, вследствие
которых возможно разрушение крепежа и потеря плотности соединений.
С другой стороны, обработка строганием заготовок из древесины
влажностью выше 20 % затруднена, а клеевые соединения получаются
непрочными.
В домашних условиях оценить влажность древесины можно при помощи
"химического" карандаша, который при излишней влажности оставляет
на заготовке чернильный след. При строгании воздушно-сухой (12-18
% влажности) древесины рубанок должен снимать тонкую непрерывную
стружку, завивающуюся в спираль. Если только что снятая стружка
легко ломается в руках,-материал пересушен. Наоборот, сырая стружка
обладает гибкостью, её влажность можно ощутить даже на ощупь.
Если деталь сделать из сырой заготовки, то при сушке размеры
ее поперечного сечения сильно изменяются. В радиальном направлении
(от сердцевины ствола дерева наружу) - размер сечения уменьшается
на 3-5%, а в тангенциальном направлении (по касательным линиям
к годичным слоям) - до 10%. Усушка вдоль волокон составляет всего
лишь 0,1-0,3 %, так что ее можно не учитывать.
В таком же процентном отношении происходит и увеличение размеров
заготовок при их разбухании.
Так
как усушка пиломатериалов в различных направлениях неодинакова,
она сопровождается их короблением - потерей плоской формы,
а иногда и растрескиванием. В наибольшей степени усыхание происходит
в пиломатериалах, вырезанных из заболонной части бревна-ближе
к коре (рис. 49). Если такая доска попадает в обшивку лодки, она
сразу жe начинает "дышать" при изменениях влажности. Поэтому желательно
подбирать доски для обшивки из частей бревна, расположенных поближе
к сердцевине, - так называемой радиальной распиловки, когда
годовые слои располагаются близко к перпендикуляру к пласти доски.
Доски тангенциальной распиловки - с расположением годовых
слоев к пласти под углом менее 60° для ответственных деталей лучше
не применять.
Древесина не обладает однородной структурой строения и нередко
включает разного рода пороки, снижающие прочность материала: сучки,
трещины, косослой, свилеватость и т. и. Для деталей набора и обшивки
необходимо отбирать наиболее качественную древесину.
Сучки, особенно выпадающие и загнившие, при заготовке
деталей должны быть удалены в отходы. В крайнем случае, сучок
можно высверлить из доски и вклеить вставку из здоровой древесины.
Если эта доска пойдет на обшивку или па настил палубы, то изнутри
на место заделки ставится накладка. Совершенно недопустимы рыхлые
и табачные сучки, представляющие собой остатки в стволе дерева
ветвей, пораженных гнилью. С этих сучков обычно начинается загнивание
остальной древесины.
Для деталей набора непригодны рейки и доски, имеющие косослой
- отклонение волокон от прямого направления, параллельного кромке
рейки, на величину более 8-10 % (8-10 мм на метр длины заготовки).
Косослой заметно снижает прочность детали и при эксплуатации судна
приводят к ее растрескиванию. В ограниченном количестве косослойные
рейки можно использовать в ламинированных деталях. Следует учитывать,
что доски из косослоя при сушке особенно сильно коробятся.
Для деталей корпуса не следует использовать доски с сердцевинной
трубкой и внутренней заболонью, которую часто можно обнаружить
в виде участков более светлого тона, чем основная древесина, на
заготовках из дуба. Эти участки легко загнивают и обладают повышенным
влагопоглощением.
Являясь материалом органического происхождения, древесина подвержена
грибковым заболеваниям, особенно при плохой защите деталей
лакокрасочными покрытиями или пластмассами. Процесс гниения быстро
распространяется по всей конструкции корпуса.
В первой начальной стадии гниения древесина изменяет свой цвет
без разрушения клеток и снижения прочности волокон. Синева,
"кофейная темнина", краснина, пятнистость -все это разновидности
начальной стадии загнивания древесины, которые должны удаляться
строганием до здоровой древесины. Гнилостные окраски, проникшие
на глубину более 2 мм, в деталях корпуса не допускаются.
Во второй стадии гниения древесина разрушается, уменьшается
ее твердость. Разновидности такой гнили - пестрая ситовая в
виде бурых участков белыми или желтоватыми пятнами, трухлявая
и белая мраморная -с темными прожилками. Пораженные ею участки
должны вырезаться в отходы вместе с прилегающими к ним участками
здоровой древесины.
Древесина, особенно если пиломатериалы вырезались из сплавных
бревен, может иметь и различного рода химические окраски (красновато-синюю,
буро-синюю, чернильные пятна, оранжевую и т. п.), которые появляются
с результате окисления дубильных веществ и химических изменений
в живых клетках. Эти виды окраски пороком не являются, и такая
древесина считается пригодной для постройки корпуса.
Заготовляя доски и рейки, следует учитывать припуск на чистовую
обработку. При строгании вручную снимается обычно 1,5-2 мм с каждой
стороны доски. Если материал заготовляется сырой, нужно предусмотреть
также припуск на усушку - около 1 мм на сторону.
Для обшивки палубы и надстроек малых судов широко применяется
фанера.
Наиболее прочной и водостойкой является бакелизированная фанера
(ГОСТ 11539-65). Она выпускается марок БФС и БФВ толщиной о, 7,
10 и 12 мм листами от 1,5 до 4,9 м длиной. Поверхность бакелизированной
фанеры покрыта слоем смолы и выглядит, как лакированная. Ею можно
обшивать не только суда с остроскулыми обводами, но и круглоскулые
корпуса, предварительно распустив лист фанеры на полосы необходимой
ширины. Бакелизированная фанера имеет большой объемный вес-до
1,2 т/м1, она тонет в воде. При окраске необходимо удалять с нее
наружный слой смолы.
Фанера марок БФС изготовляется с применением спирторастворимых
смол; у БФВ-1 средние слои склеены водорастворимыми смолами, а
рубашки припитаны спирторастворимыми смолами; фанера марки БФВ-2
изготовляется полностью на водорастворимых смолах. Фанеру марки
БФС можно склеивать как по пласти, так и "на ус"; листы марок
БФВ рекомендуется склеивать только по пласти (с применением стыковых
накладок), так как при склеивании "на ус" не достигается необходимая
прочность соединения.
Авиационная березовая пятислойная фанера БС-1, БП-1 и
БПС-1 [ГОСТ 102-49) также обладает высокой прочностью и водостойкостью.
Она легче бакелизированной. Слои этой фанеры склеены бакелитовой
пленкой и смолой С-1. Изготовляется в листах от 0,8 X 1,0 до 1,5Х
1,5 м толщиной от 1 до 12мм
Для корпусов небольших моторных лодок при условии тщательного
покрытия корпуса (лучше-оклейки стеклопластиком) может быть применена
строительная фанера ФСФ или ФК по ГОСТ 3916-69.
Достаточной водостойкостью может обладать и декоративная
фанера, которой любители обшивают лодки, обращая ее окрашенной
стороной внутрь корпуса.
В том случае, когда марка фанеры неизвестна, ее пригодность
для постройки судна можно установить по следующим признакам. У
фанеры, склеенной белковым альбуминным клеем, в расщепе между
слоями видны буро-черные ноздреватые его следы. Такая фанера абсолютно
непригодна для конструкций, которые соприкасаются с водой. У фанеры,
склеенной казеиновым клеем, слой клея плотный, роговидный, светло-серого
цвета. Такая фанера может применяться для внутреннего оборудования
катера или лодки.
Фанера, изготовленная на смоляных клеях, наиболее водостойка.
Цвет клеевого слоя у такой фанеры или коричневый, или буро-красный.
Можно убедиться в водостойкости фанеры, замочив образец ее на
сутки в воде и прокипятив его затем в течение часа. После этого
прочность испытуемого образца на отрыв слоев не должна заметно
ухудшаться.
Для большей гарантии фанеру неизвестной марки следует пропитать
горячей олифой. В крайнем случае, для обшивки судна можно применить
обычную строительную фанеру, но пропитанную олифой. Поверхность
фанеры покрывается натуральной олифой и проглаживается утюгом,
нагретым до температуры 150- 200 0С. Процедура повторяется до
тех пор, пока фанера не перестанет впитывать олифу. Обычно это
происходит после третьей пропитки. Внутреннюю сторону обшивки
надо пропитать до установки на набор, наружную -после. На пропитанной
олифой фанере слой краски держится плохо, особенно у шляпок гвоздей
и шурупов, головок болтов (если они не утоплены в обшивку). Поэтому
слой краски рекомендуется армировать тканью.
Строительную фанеру, пропитанную олифой, лучше всего оклеить
тонкой стеклотканью на эпоксидном связующем или на лаке 6с или
6т (ГОСТ 5470-50). Годится также и обычная марля. Оклейка производится
таким образом: на пропитанную олифой фанеру наносится слой лака;
через несколько часов, когда лак загустеет, на него накладывается
ткань, которая приглаживается торцовочной кистью (кисть надо периодически
смачивать скипидаром); после нескольких дней сушки поверхность
снова покрывается слоем лака, затем сушится. Высохшую поверхность
можно шпаклевать, шкурить и красить.
Оклеивать обшивку рекомендуется с двух сторон, причем внутреннюю
поверхность нужно оклеивать до установки набора. Оклейку можно
производить на нитроэмалевой или нитроглифталевой краске с применением
более плотных сортов материи - бязи и миткаля. Для этого грунтованная
жидкой краской фанера после высыхания покрывается толстым слоем
густой нитрокраски. Затем на фанеру накладывается ткань, которая
с торцов при помощи кисти смачивается растворителем для нитрокраски.
После просушки поверхность можно шпаклевать и красить.
§ 2. Крепежные детали
Основным крепежом, с помощью которого любитель
соединяет детали в узлах корпуса лодки, служат гвозди и шурупы.
В судостроении используют обычно гвозди-заклепки из красномедной
проволоки и латунные шурупы или стальной оцинкованный крепеж.
Красномедные гвозди в продажу не поступают,
но их несложно сделать самому из медной проволоки в специальном
приспособлении - гвоздильне. Она состоит из двух стальных планок
1, приваренных к дужке 2 из проволоки (рис. 50). В планках, соединенных
вместе, просверливают отверстия диаметром на 0,1-0,2 мм меньше
диаметра проволоки. Для образования шляпки на одном конце отверстий
делают зенковку.
Нарезанные по размеру гвоздей куски проволоки 3
вставляют в отверстия так, чтобы над планкой возвышался конец
в 5-6 мм, после чего гвоздильню зажимают в тиски 4. Из выступающей
части проволоки легкими ударами ручника делают шляпку гвоздя.
Удары наносят попеременно тупым и заостренным концом молотка.
Металл должен заполнить луночку гвоздильни равномерно и без разрывов.
Острые концы гвоздей можно слегка заточить на наждаке, имея в
виду, что гвозди, как правило, забивают в заранее рассверленное
отверстие (диаметр сверла-на 0,1 мм меньше диаметра гвоздя). Только
под гвозди диаметром менее 2,5 мм отверстия допускается не сверлить,
поэтому концы таких гвоздей следует заострить нормальным образом.
Для запрессовки клеевых соединений деталей набора
с фанерными кницами, флорами и т. п. можно использовать сапожные
латунные гвозди 2Х 16, поступающие в продажу.
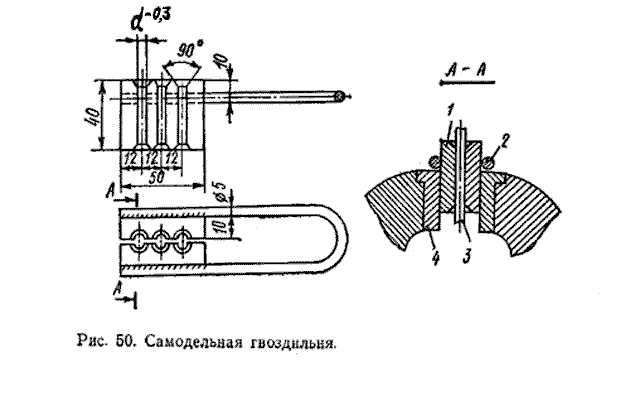
Обычные стальные шурупы и гвозди, купленные в магазине,
можно сдать для оцинковки в мастерские, которые есть в
любом городе. Существует также способ горячей оцинковки в условиях
самодеятельной верфи. Для этого надо иметь коксовый горн, стальной
ковш (или тигель) и клещи. Перед оцинковкой детали очищают от
грязи, ржавчины и окалины металлическими щетками, а затем протравливают
в растворе соляной кислоты. После этого детали промывают в теплой
воде и опускают на несколько секунд в хлористый цинк, не прикасаясь
к ним руками. Затеи крепеж сушат и приступают к оцинковке, которую
можно делать двумя способами.
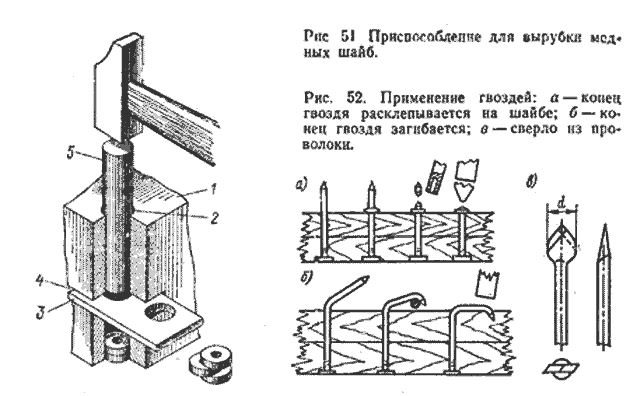
При первом способе в расплавленный в тигле цинк
добавляют десятую долю чистого олова, затем бросают в тигель немного
нашатыря и через его пленку погружают в раствор оцинковываемую
деталь.
При втором способе деталь предварительно опускают
на 2-3 секунды в крепкий раствор нашатыря, стряхивают раствор
до последней капли, а затем медленно и осторожно погружают деталь
в расплавленный цинк. Этот способ опасен тем, что случайно оставшаяся
капля нашатыря может вызвать выплескивание металла из тигля. Когда
поверхность деталей сплошь покроется ровным слоем цинка, их бросают
на пол, чтобы при ударе с них слетели излишки расплавленного цинка.
Оцинковывать детали надо обязательно в защитных очках, в брезентовом
костюме и в перчатках.
На худой конец, можно употребить и неоцинкованный
крепеж, но его надо предварительно накалить до вишневого цвета
и опустить в олифу. В крайнем случае, до установки крепеж можно
опустить в лак, густую краску или олифу. Однако рассчитывать на
долгую жизнь лодки, построенной на таком крепеже, не приходится.
При постройке малых судов на верфях концы гвоздей-заклепок
расклепывают на красномедных шайбах. Подобные же шайбы
можно сделать самому при помощи несложного приспособления (рис.
51). Делается оно из стального бруска 1, в котором сверлят отверстие
2 диаметром, равным диаметру шайбы. От края бруска перпендикулярно
оси отверстия делают прорезь 4 шириной в две толщины металла,
из которого изготовляются шайбы. В верхнюю часть вставляют стальной
пуансон (пробойник) 5, имеющий диаметр на 0,2-0,5 мм меньше диаметра
отверстия 2. В прорезь закладывают полосу или кромку листа 3,
из которого вырубаются шайбы. Вырубка производится легкими ударами
молотка по пуансону. Верхняя часть канала в бруске служит направляющей
для пуансона, нижняя -накопителем для шайб.
Отверстия в шайбах можно просверлить или вырубить
таким же способом, для чего необходимо сделать еще один канал
в бруске, причем его нижняя часть-под полосой, из которой вырубаются
шайбы, должна иметь соответствующий диаметр, а нижний конец пробойника
должен быть проточен по диаметру отверстия в шайбе.
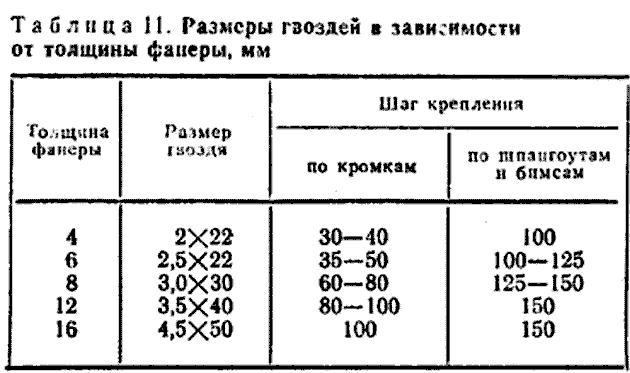
При использовании гвоздей их ставят таким
образом, чтобы расстояние от кромки доски до гвоздя было не менее
3 его диаметров, а от торца доски до гвоздя - не менее 6d. Если
вдоль кромки доски забивают несколько гвоздей, их нужно ставить
не по одной прямой, а в шахматном порядке, чтобы не расколоть
доску по годичному слою.
Гвоздь может быть вбит (через заранее просверленное
отверстие) в дерево или же пробит сквозь скрепляемые детали. На
вышедший конец гвоздя надевают шайбу, осаживают ее до плотного
прилегания к поверхности детали при помощи обжимки или трубки
подходящего диаметра, конец гвоздя откусывают, оставляя 2-3 мм
на расклепывание. Расклепывают конец гвоздя, нанося легкие удары
попеременно то плоской, то острой частью молотка до тех пор, пока
образующаяся головка не закроет внутреннего диаметра шайбы. Со
стороны шляпки при этом гвоздь поддерживают стальным бруском пли
тяжелым молотком (рис. 52,а).
Конец гвоздя можно также загнуть и утопить его
в древесину (рис. 52,6). Важно, чтобы гвоздь был сильно подтянут
к слоям дерева. Во всех случаях головки гвоздей утапливают в древесину.
Для просверливания отверстий под гвозди удобно пользоваться
не обычным сверлом, которое легко сломать, а сделанным из гвоздя
или стальной проволоки. Конец гвоздя расплющивается и затачивается,
как показано на рис. 52, в. Ширина расплющенной части должна быть
равна диаметру отверстия, которое надо будет просверлить.
Рекомендуемые размеры гвоздей для крепления фанерной
обшивки к набору приведены в табл. 11.
Под шурупы с потайной головкой отверстия
сверлят двумя сверлами: под нарезанную часть шурупа-диаметром
А, под гладкую часть-диаметром Б и под головку -зенковкой диаметром
В (рис. 53, а). Диаметр отверстия А подбирается в зависимости
от твердости древесины. Например, для шурупа диаметром 4 мм в
дубе нужно сверлить отверстие А диаметром 3,2 мм, в сосне- 2,5
мм. Глубина и диаметр отверстия Б подбираются по гладкой части
шурупа. Для 4-миллиметровых шурупов, например, этот диаметр принимается
равным 3,8- 3,9 мм. Существуют специальные сверла, сделать которые
стоит для наиболее ходовых размеров шурупов, если их несколько
сотен. Шурупы не должны проходить насквозь; они должны быть короче
суммарной толщины соединяемых деталей, по крайней мере, на 3 мм.
При
завинчивании шурупов нельзя допускать их проворачивания и перекоса
в отверстии; не следует также забивать их ударами молотка; молотком
можно лишь ввести шуруп в отверстие и придать ему нужное направление.
Для облегчения работы шурупы можно заворачивать коловоротом или
дрелью со вставленной в патрон вместо сверла отверткой.
Рекомендуемые размеры шурупов и шаг в соединениях
для лодок с фанерной обшивкой приведены в табл. 12.
Для соединения отдельных деталей корпуса могут применяться
болты. Диаметр болта d должен быть равен примерно 15 % его длины.
При установке болтов вдоль волокон расстояние между их осями выдерживается
не менее 6d, а при расположении поперек-не менее 3J. Расстояние
от оси болта до кромки доски должно быть не менее 2,5d, а до торца-не
менее (6 - 8)d.
Головки болтов, шурупов и гвоздей утапливают ниже
поверхности наружной обшивки на 1,5-2 мм. Углубление затем шпаклюют
древесной мукой (или опилками), замешанной на клее ВИАМ Б-3 или
на эпоксидной смоле. В обшивке из досок головки шурупов могут
быть заделаны деревянными пробками. Вытачивают пробки при помощи
полого сверла из той древесины, в которую они будут ставиться.
Забиваются пробки с натягом 0,5-0,8 мм в тщательно очищенные отверстия.
Направления волокон древесины у забитой пробки и у доски обшивки
должны совпадать для возможности се обработки строганием
В тех случаях, когда есть опасность расколоть деталь,
ставя в нес рядом несколько шурупов или гвоздей, лучше располагать
их в шахматном порядке, по разным слоям древесины с расстоянием
между ними в 2-4 диаметра.
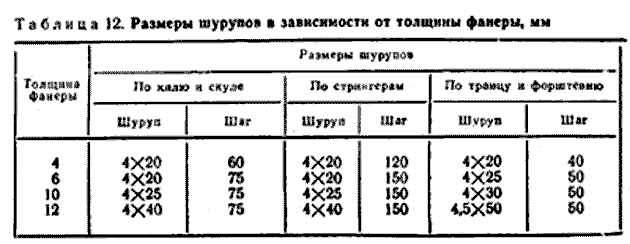
§ 3. Клеи и склеивание
Клеи. Для склеивания основных деталей корпуса
(форштевней, обшивки, палубы и т. п.) необходимы водостойкие смоляные
клеи, такие, как ВИАМ Б-3, КБ-3, КДМ-6, эпоксидные.
ВИАМ Б-3 - водо-, масло- и бензостойкий
фенолформальдегидный клей холодного отверждения. Его основным
компонентом является фенольно-баритовая смола ВИАМ Б, которую
перед склеиванием разжижают техническим ацетоном или спиртом-сырцом.
Отвердителем является керосиновый контакт 1-го сорта (контакт
Петрова). Для приготовления клея в 100 вес. ч. смолы добавляют
10 вес. ч. ацетона или спирта, перемешивают, добиваясь равномерного
растворения смолы, затем вливают керосиновый контакт в количестве
16-20 вес. ч. Более точно необходимое количество контакта можно
определить, разделив 1400 на кислотное число контакта. Клей с
введенным контактом тщательно перемешивают примерно в течение
10 мин. до получения однородной смеси. Вязкость клея должна быть
такой, чтобы он стекал с палочки (мешалки) тонкой непрерывной
струёй. Клей, приготовленный таким образом, годен к употреблению
в течение 2-4 часов, поэтому готовить его нужно небольшими порциями.
Необходимое количество клея можно определить из расчета его расхода
при нанесении на одну поверхность 180-250 г/м2 на обе - 250-300
г/м2.
При работе с этим клеем следует иметь в виду, что
смола выделяет фенол- токсичное вещество, вредно действующее на
органы дыхания и кожу, поэтому все работы нужно вести на открытом
воздухе или в хорошо вентилируемом помещении.
В продажу поступает эпоксидный клей ЭД-5,
который приготавливается из смолы ЭД-5 (100 вес. ч.) и отвердителя-полиэтиленполиамина
(6,5 вес.ч.). Приготовляют клей небольшими порциями (он действует
в течение 45-75 мин.), вливая в смолу полиэтиленполиамин и тщательно
перемешивая смесь в течение 5-7 мин. Если клей получается слишком
вязким, в него можно ввести немного растворителя - толуола, ацетона
или спирта.
Достоинством эпоксидного клея является сравнительно
небольшое давление; запрессовки - не более 0,5 кгс/см2. Расход
эпоксидного клея примерно такой же, как и ВИАМ Б-3.
Для склеивания деталей корпуса можно применять
также эпоксидный компаунд К-153, чехословацкую эпоксидную смолу
"Э п о к с и - 2000", клей "Киттифакс". При хорошей подгонке склеиваемых
деталей возможно применение поливинилацетатного клея ПВА. Клей
ПВА наносят на обе склеиваемые поверхности тонким слоем; после
открытой выдержки в течение 5 мин. детали складывают вместе и
через 10 мин. закрытой выдержки создают давление-не более 0,5
кгс/см2. Продолжительность склеивания зависит от температуры воздуха
и колеблется от 1-2 ч до суток.
Клей К-17 приготовляют из смеси мочевиноформальдегидной
смолы МФ-17 (100 вес. ч.) с древесной мукой (8 вес. ч.); отвердителем
служит 10 %-ный раствор щавелевой кислоты в воде. Количество воды
регулируется в зависимости от требуемой вязкости клеевого раствора.
Клей применяют после тщательного перемешивания; действует он в
течение 2-6 ч.
Для деталей, непосредственно не соприкасающихся
с водой (рангоут, внутреннее оборудование), могут применяться
казеиновые клеи. Они выпускаются следующих марок: В-105, В-107
и ОБ. Лучшим является клей марки В-105. Для приготовления раствора
казеинового клея порошок казеина разводят в чистой питьевой воде
комнатной температуры при соотношении его с водой как 1: 1,7 или
1: 2, в зависимости от требующейся начальной вязкости. Клеевой
раствор сохраняет рабочую вязкость в течение не менее 4 ч после
приготовления. Для ее сохранения воду, используемую для растворения
порошка, рекомендуется летом охлаждать до 10°С, а при работе в
холодном помещении (в пределах от +6 до +15°С) употреблять подогретую
до +25 °С. Клей нужно наносить на обе поверхности из расчета 700-1000
г/м2 (230-340 г сухого порошка). Заготовки, покрытые клеем, выдерживают
на воздухе 2-5 мин., затем соединяют. Закрытая пропитка продолжается
5-20 мин., после чего склеиваемые детали запрессовывают. Продолжительность
выдержки под давлением при склеивании без нагрева составляет:
для прямолинейных деталей-6-8 ч, для изогнутых- 10-18 ч. Обработка
деталей возможна через 2-3 ч после снятия давления.
В крайнем случае, казеиновый клей можно использовать
и для склеивания деталей набора самых маленьких лодок. После склеивания
надо тщательно защитить поверхности деталей, особенно в районе
клеевого соединения, от влаги, пропитав их горячей олифой или
покрыв лаком. Водостойкость клея можно повысить, введя в него
портландцемент и антисептик. На 100 вес. ч. клея В-107 (в порошке)
добавляют 75 вес. ч. цемента марки 200 и выше и 3 вес. ч. динитрофенола
или оксидифенола. Цемент нужно применять самого тонкого помола
и без посторонних примесей.
Заготовки и детали для склеивания любым клеем должны
быть соответствующим образом подготовлены. Влажность древесины
не должна превышать 12-18%; склеиваемые поверхности нужно тщательно
подогнать, прострогать и очистить от грязи. Нужно помнить, что
чем тоньше будет слой клея, тем прочнее соединение. Толщина клеевой
пленки не должна превышать 0,3-0,5 мм.
Смоляной клей наносят на обе поверхности кистями,
тонким слоем. Сквозь клей должна быть видна текстура древесины.
Этот первый слой впитывается древесиной, поэтому нужно выдержать
заготовки в течение 5-10 мин., затем нанести второй слой и соединить
детали, прижимая их друг к другу с помощью струбцин, цвинок или
грузов таким образом, чтобы создать давление от 2 до 4кгс/см2
.В некоторых случаях требующееся давление запрессовки обеспечивается
гвоздями и шурупами. Необходимое для этого количество крепежа
можно прикинуть из расчета, что один шуруп диаметром 3-4 мм и
длиной 25-30 мм создает местное давление 50-70кгс; один гвоздь
2 Х 20 - около 20кгс.
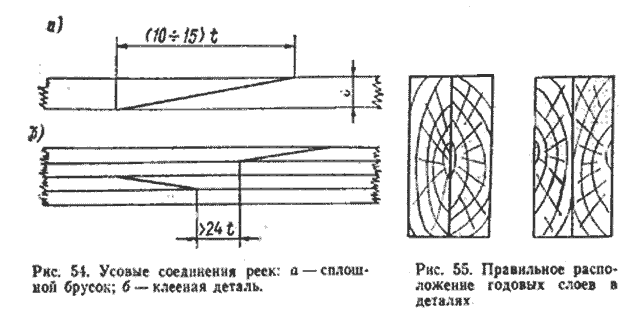
Детали под давлением выдерживают в течение 15-20
ч; обрабатывать же их следует не ранее, чем через сутки после
склеивания. Клеить в сырую, холодную погоду, в туман и дождь нельзя.
Лучше всего это делать при комнатной температуре и влажности воздуха
примерно 60 %. Для ускорения полимеризации клея запрессованные
детали можно подогревать до температуры 50-60 0 С, например, при
помощи отражательных электрогрелок- рефлекторов.
Клеевые соединения. Использование клея существенно
расширяет возможности судостроителя-любителя. Клеевые соединения
позволяют применять для изготовления многих длинных деталей (поясья
наружной обшивки, детали продольного набора и т. п.) короткомерный
материал, удалять из заготовок пороки древесины. При помощи клея
проще обеспечить плотность и водонепроницаемость тех узлов, где
эти качества особенно важны. Не составляет труда получить детали
большого поперечного сечения, набрав их в виде пакета склеенных
между собой реек. Используя тонкие рейки, можно изготавливать
детали большой кривизны без предварительного распаривания заготовок.
Для повышения прочности отдельных деталей, подверженных большим
переменным нагрузкам (фундаментные балки под двигатель, флоры,
шпангоуты) их можно оклеить по пластям слоями фанеры, что предотвратит
растрескивание древесины.
Наиболее распространенным способом соединения деталей
по длине является склеивание "на ус" (рис. 54).
Стыкуемые концы деталей сострагивают при этом под одинаковым углом.
Длина заусовки принимается равной 10-15 толщинам стыкуемых реек.
Подобные усовые соединения применяются при изготовлении гнутоклееных
деталей, мачт и других брусьев, собираемых из нескольких слоёв
по толщине. При этом стыки в соседних слоях разносят один от другого
на расстояние не менее 24 толщин рейки. Смежные рейки следует
располагать так, чтобы сторона одной рейки, ближайшая к наружному
диаметру сечения ствола дерева (заболонная часть) прилегала к
такой же стороне другой (или наоборот- сердцевина к сердцевине).
Это нетрудно установить по годовым слоям (рис. 55).
При выполнении усового соединения на стыкуемых концах
реек или досок размечается длина заусовки; затем основную часть
древесины удаляют на дисковой или ленточной пиле или же стесывают
топором. Потом обе рейки укладывают рядом на верстак, закрепляют
их при помощи струбцин таким образом, чтобы концы реек совпали
с торцом верстака, и обрабатывают склеиваемые поверхности полуфуганком
за один проход (рис. 56). Это гарантирует идентичный угол заусовки
на обоих концах и плотность прилегания поверхностей. Если одновременно
готовятся к склейке несколько реек, каждую пару следует пометить.
При склеивании обе поверхности намазывают клеем
и после выдержки запрессовывают при помощи струбцин. Для равномерного
распределения давления с обеих сторон стыка под зажимы струбцин
подкладывают обрезки досок соответствующих размеров. А чтобы подкладки
случайно не приклеились к рейкам; под них можно положить полиэтиленовую
пленку, кальку или просто газету.
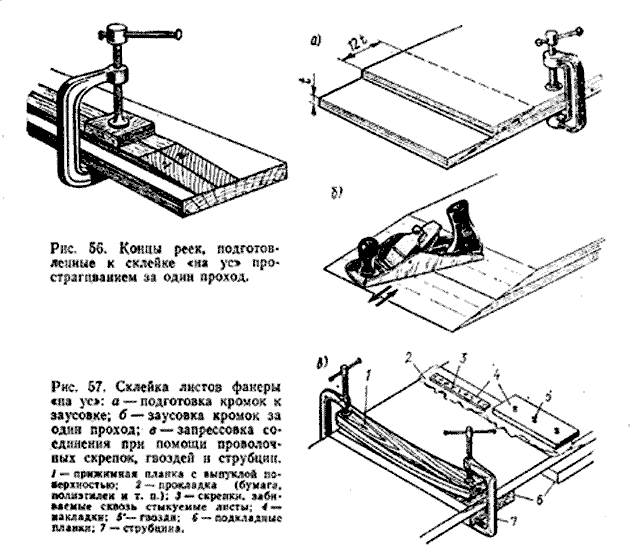
При аккуратном исполнении усовое соединение имеет
прочность не ниже основного материала рейки.
Подобное же соединение применяется и для сращивания
листов фанеры, причем для достижения высокой прочности длина заусовки
принимается равной 12- 20 толщинам фанеры. Стыкуемые кромки также
следует обрабатывать совместно. Для этого обе кромки фанеры укладывают
у торца верстака так, чтобы верхняя кромка отступала от нижней
на величину заусовки (рис. 57). Если склеивают толстую фанеру,
нелишне проверить толщину обеих кромок, поскольку листы изготовляются
с известными допусками по толщине. На верхнем листе ширину, заусовки
прочерчивают при помощи линейки. Закрепив листы к верстаку парой
гвоздей, прострагивают кромки под нужным углом острым полуфуганком.
По мере снятия древесины будут появляться слои шпона, которые
должны быть параллельными кромкам и иметь одинаковую ширину. Строгать
нужно, располагая рубанок под небольшим углом к кромке фанеры,
чтобы древесина из нее срезалась, а не выкрашивалась.
Важно, чтобы получился острый край, который при
склеивании хорошо пропитывается клеем и обеспечивает ровную поверхность
фанеры. Притупленная кромка листа в клееном соединении недопустима,
так как через нее в слоя попадает вода; кроме того, соединение
получается более слабым.
При склеивании важно обеспечить надежную фиксацию
обеих кромок таким образом, чтобы они не скользили относительно
друг друга при приложении давления. Стык помещают между двумя
двухдюймовыми досками, пластям которых, прилегающим к фанере,
нужно придать небольшую выпуклость. Струбцины можно поставить
только вблизи от продольных кромок листов, поэтому при зажатии
струбцин выпуклость досок позволяет распределить давление запрессовки
более равномерно по ширине листа. Хорошо перед запрессовкой вбить
пару гвоздей через обе соединяемых кромки с тем, чтобы они не
сдвинулись. Между досками и фанерой прокладывают полиэтилен или
бумагу.
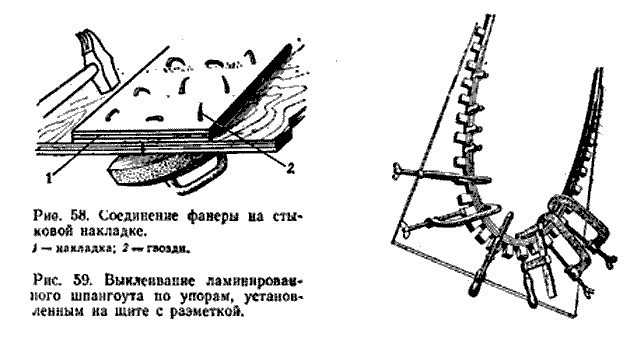
Более простое соединение фанерных листов, по менее
надежное и обладающее определенными конструктивными недостатками,
- это на стыковой планке - накладке (рис. 58). Планка вырезается
шириной 100-120 мм из такой же фанеры, что и соединяемые листы,
и накладывается на стык с внутренней стороны обшивки. Сопрягаемые
поверхности, в том числе и торцы стыкуемых листов, намазывают
клеем и запрессовывают при помощи грузов (мешки с песком, ведра,
кирпичи и т. н.) или мелких гвоздей, концы которых загибают, подложив
под шляпки металлическую плиту.
При выполнении этого соединения необходимо только
прострогать склеиваемые поверхности и торцы фанеры, однако при
простоте самого соединения оно усложняет последующие работы, но
сборке корпуса: поскольку накладки являются местными утолщениями
листов обшивки, под них приходится делать выемки в рейках продольного
набора днища и бортов. Кроме того, при растяжении состыкованного
листа возможно возникновение усилий, действующих перпендикулярно
поверхности склейки, т. е. - на отрыв, к чему клеевой слой довольно
чувствителен. Это следует иметь в виду и при выполнении различных
угловых соединений, где используются кницы: лучше поставить две
кницы (с обеих сторон шпангоута), чем одну.
Соединение листов фанеры со стыковой планкой часто
применяется без склеивания. В таких случаях между накладкой и
стыкуемыми листами прокладывается слой миткаля, пропитанного краской.
Гнутоклееные детали. В корпусе малого судна
есть немало деталей, имеющих криволинейную форму, таких, как форштевни,
бимсы, привальные брусья, шпангоуты. Их можно сделать гнутоклееными
(иногда такие детали называют ламинированными) из пакета
тонких реек. Каждой рейке несложно придать требуемый изгиб, а
затем склеить их. После затвердевания клея вся деталь сохраняет
заданную форму.
В зависимости от габаритных размеров выклеиваемой
детали делают заготовки из досок (толщиной 8-10 мм), реек (4-7-миллиметровых)
или фанеры. Ширину заготовок следует брать на 4-6 мм больше, чем
ширина, которую необходимо получить после окончательной обработки.
Из досок (или толстой фанеры) делают шаблон - цулагу, соответствующий
по форме и размерам обводам будущей детали; контуры шаблона снимают
с плаза, Шаблон прибивают гвоздями к полу. На расстоянии от шаблона,
немного большем толщины детали, закрепляют прижимы или прибивают
упоры для клиньев или цвинок.
Заготовленные и выстроганные заранее планки намазывают
клеем и запрессовывают в один пакет, прижимая его струбцинами,
цвинками или клиньями к шаблону (на рис. 59 форма детали задается
брусками, закрепленными на щите). Можно для запрессовки использовать
заклепки, шурупы, гвозди, если только они не послужат помехой
при дальнейшей обработке детали.
Размечая шаблон, нужно учесть, что после снятия
с него склеенной детали она немного распрямится. Поэтому шаблон
нужно сделать с несколько меньшим радиусом кривизны. Например,
выклеивая форштевень для лодки с высотой борта в носу 800 мм.
нужно верхнюю точку штевня на шаблоне перенести внутрь корпуса
на 50-60 мм.
При выполнении гнутоклееных деталей следует учитывать
также, что радиус изгиба не должен быть меньше значений, указанных
в табл. 13.
В
таких деталях удобно применять рейки из различных пород древесины.
Например, наружные рейки на форштевне сделать дубовыми, а внутренние
- из сосны.
Несложно выполнить ламинированными скуловые стрингера,
привальные брусья и другие детали набора, имеющие крутой или сложный-в
двух направлениях-изгиб, непосредственно на стапеле во время сборка
корпуса. Сначала на место укладывают первую рейку, крепят ее к
шпангоутам и форштевню, затем, смазав клеем сопрягаемые поверхности,
на нее накладывают вторую и последующие слои по толщине. Вместе
со струбцинами для запрессовки таких деталей можно использовать
обычные неоцинкованные (как их называют - "черные") гвозди и шурупы,
которые по окончании полимеризации клея из детали удаляют, а отверстия
заделывают "чопиками" на клею.
Ламинированными рекомендуется выполнять также детали,
которые нельзя сделать из доски без перетеса волокон древесины
- кнопы, старнкницы, брештуки и т. п. Иногда достаточную прочность
подобных деталей удается получить и за счет фанеровки - оклейки
доски с обеих сторон фанерой.
Несколько советов по применению клеев. При
небольших размерах склеиваемых поверхностей клей на них наносят
при помощи палочки сечением у рабочего конца около 2 >< 20 мм.
Если поверхность велика, клей можно на нее налить, а затем равномерно
распределить при помощи палочки, резинового шпателя или валика.
Необходимо обеспечить топкий равномерный слой клея по всей поверхности.
Излишки клея выдавливаются под давлением, но все равно толстый
клеевой слой является слабым местом соединения. Недостатком является
и слишком тонкий слой, который не обеспечивает надежного насыщения
открытых клеток древесины в обеих деталях.
Давление не должно быть чрезмерным, чтобы не выдавить
из соединения почти все количество нанесенного на поверхности
клея. Особенно это следует учитывать при использовании винтовых
струбцин.
Выступивший из стыка клей необходимо удалять сразу
же, не ожидая его затвердевания. Сделать это можно при помощи
влажной тряпки. В крайнем случае, можно дождаться желатинизации
клея до консистенции студня и счистить его шпателем или стамеской.
Особенно это важно сделать на ламинированных деталях, у которых
довольно много клея выступает по слоям, обработка деталей с затвердевшим
клеем приводит к необходимости частой заточки режущего инструмента
и нередко - к его порче.
Для ускорения затвердевания клея можно применять
подогрев, направляя вентилятором горячий воздух от электрогрелок
на склеенные детали, используя низковольтные нагревательные элементы
или рефлекторы. Если лодка строится в неотапливаемом помещении,
то на ночь корпус на стапеле можно закрыть чехлом, оставив под
ним включенной 100-ваттную электролампу-выделяемого ею тепла будет
достаточно, чтобы поддерживать температуру немного выше, чем в
помещении.
§ 4. Стеклопластик
Стеклопластик - искусственный слоистый материал,
получаемый на основе связующего из синтетических смол и армирующих
стекломатериалов. В любительском судостроении стеклопластик широко
используется для оклейки корпусов, построенных из дерева или фанеры,
а также в виде композитных конструкций, когда прочность корпуса
и водонепроницаемость его обеспечивается обшивкой и палубой из
стеклопластика, а форму корпусу придают легкие конструкции из
листовых материалов (фанеры, стеклотекстолита, картона) или пенопласта.
Для приготовления связующего применяются полиэфирные
смолы марок ПН-1, ПН-2, ПН-3 и ПH-6; бесстирольные полиэфирные
смолы НПС-609-21, НПС-609-22, ПН-62; эпоксидные смолы ЭД-5, ЭД-6
н эпоксидные компаунды К-54/6, К-55/6, К-115 и т. п. Рецептура
связующего на основе этих смол представлена в табл. 14.
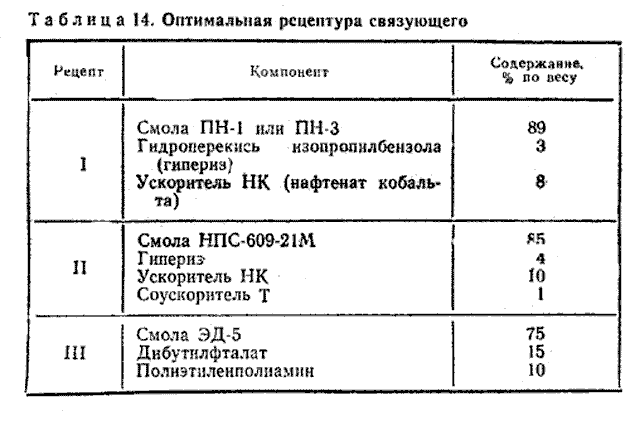
В качестве отверждающей добавки (инициатор) в полиэфирные
смолы вводится гидроперекись изопропилбензола (гипериз). Смола
с гиперизом затвердевает в течение нескольких часов, поэтому для
ускорения процесса в нее вводят ускоритель-нафтенат кобальта (8
вес. ч. 10 %-НОГО раствора в стироле). При приготовлении связующего
сначала вводят ускоритель и только после хорошего (в течение 10-15
мин.) перемешивания-гипериз. Состав снова хорошо перемешивают.
Ускоритель и инициатор не должны соединяться непосредственно,
так как при этом может произойти взрыв.
При использовании эпоксидных смол ЭД-5 и ЭД-6 в
смолу добавляют дибутилфталат (15 вес. ч. на 100 вес. ч.), с которым
она может храниться длительное время. Ускорителем служит полиэтиленполиамин
(10 вес. ч.), который вводят непосредственно перед оклейкой корпуса.
При смешивании связующего с полиэтиленполиамином выделяется тепло;
вследствие этого смесь может быстро отвердеть. Поэтому ускоритель
рекомендуется вводить частями при хорошем перемешивании.
Если работу по формованию корпуса ведут при температуре
ниже +18'С, в связующее можно ввести соускоритсль-диметиланилин
в количестве 0,025-0,1 % от веса смолы. Он резко ускоряет желатинизацию
смолы.
Связующее следует готовить в количестве, которое
может быть израсходовано за 1,5-2 ч работы. Готовят связующее
в эмалированной посуде. Использовать медную, латунную или гуммированную
посуду нельзя, так как эти материалы могут отрицательно повлиять
на отверждение связующего.
Если предстоит формовать или оклеивать вертикальные
борта либо днище в "потолочном положении", то за несколько часов
до начала оклейки в смолу порциями вводят, при тщательном перемешивании,
приготовленную дозу тиксотропного наполнителя-белой сажи марок
У-333 или А-5 (7 °/о от веса смолы) либо аэросила (1-1,5 %). Наполнитель
повышает вязкость смолы, предотвращает подтеки связующего. Через
2ч смолу с введенным наполнителем еще раз тщательно перемешивают
и уже передсамым началом работы отвешивают и смешивают между собой
необходимое количество смолы, ускорителя и инициатора.
В промышленности для постройки пластмассовых судов
применяют специальные стекловолокнистые армирующие материалы,
подвергнутые гидрофобной обработке.
Самый плотный и прочный стеклопластик при малых
толщинах (от 3 до 6 мм) получается при использовании стеклотканей
сатинового переплетения Т-11-ГВС-9 по ГОСТ 19170-73. При собственной
толщине около 0,3 мм один слой такой ткани в обшивке лодки дает
толщину 0,4-0,5 мм, поэтому при формовании корпуса требуется уложить
довольно значительное число слоев ткани. Выходом из положения
является укладка внутренних слоев из более толстой жгутовой
ткани-стеклорогожи, которая сплетается из толстых пучков стеклонитей
и потому несколько хуже пропитывается связующим. Наиболее употребительны
для корпусов малых судов стеклорогожи ТР-056-ГВС-9 и ТР-07-ГВС9,
выпускаемые по ОСТ 6-11-209-74. В обшивке слой такой ткани дает
до 1-1,2 мм толщины. Нужно, однако, иметь в виду, что толстые
жгутовые ткани могут быть уложены на поверхности, сопрягаемые
под определенным минимальным радиусом, а при недостаточно тщательной
пропитке и слабом прикатывании слоев по оснастке наружная обшивка
может фильтровать воду. От последнего недостатка можно избавиться,
если использовать оба типа тканей в комбинации: наружный слой
обшивки-сатиновая ткань, два слоя жгутовой ткани, прокладочный
слой сатиновой ткани, два слоя ТР, внутренний слой-сатиновая ткань.
Палубу можно формовать из трех-четырех слоев стеклорогожи, заключенных
между наружными слоями сатиновой ткани.
Для наружного слоя используется и еще более тонкая
стеклоткань полотняного переплетения - стеклосетка СЭ-01
по ТУ6-11-321-74. Благодаря малой толщине и хорошей проницаемости
для связующего она выравнивает поверхность, скрадывает грубую
текстуру стеклоткани и хорошо держит наружный-декоративный слой
окрашенного связующего.
Большое влияние на прочность стеклопластика оказывает
соотношение (по весу) количества смолы и стекломатериала. С уменьшением
количества смолы прочность стеклопластика сначала возрастает,
а затем при малом ее содержании-плохой пропитке стеклонитей -
начинает уменьшаться. Оптимальным является содержание в пластике
45-50 % смолы и 55-50 % армирующего стекломатериала.
Любителям иногда приходится иметь дело со стеклотканями
неизвестных марок и специального назначения. Следует иметь в виду,
что в процессе изготовления стеклоткань обычно смачивается масляной
эмульсией или парафиновым раствором; это делает ее непригодной
для пропитки связующим. Поэтому перед использованием стеклоткани
необходимо удалить замасливатель, промыв ткань бензином (это нельзя
делать в ванной комнате и в других помещениях небольшого объема!).
Другие виды замасливателей снимаются уайт-спиритом или ацетоном.
Промытую ткань следует просушить в течение 2-4 ч, лучше всего
на открытом воздухе.
Электроизоляционные ткани марок ЛСМ, АСМИ, ЛСЭ,
ЛСБ и ЛСК выпускаются пропитанными синтетическими смолами и для
оклейки корпусов практически непригодны. Большинство из этих тканей
можно отличить по окраске в желтый или бордовый цвет и по наличию
пропитки.
Постройка, или формование, пластмассового
корпуса лодки производится в матрице - обычно разъемной
по килю наружной форме корпуса. Поверхность матрицы тщательно
шпаклюется и полируется, благодаря чему наружные поверхности корпуса
лодки получают блестящую глянцевую поверхность. При формовании
на матрицу сначала наносят разделительный слой, например,
из поливинилового спирта или воска, который обеспечивает свободное
отделение готовой обшивки от поверхности матрицы. Затем наносят
декоративный слой связующего с пигментом для окрашивания
этого слоя в желаемый цвет. После желатинизации декоративного
слоя начинается формование обшивки, которое состоит в последовательной
укладке слоев армирующей стеклоткани и тщательной прикатке их
валиками к поверхности формы. В зависимости от толщины армирующей
ткани таких слоев укладывают 4-8 (для корпусов длиной до 6 м).
Общая толщина обшивки легких пластмассовых гребных лодок составляет
2,5-3 мм; глиссирующих корпусов длиной до 5 м-4-6 мм; более крупных
водоизмещающих катеров и яхт длиной до 8 м -6-10 мм.
Большим достоинством стеклопластика является возможность
изготовления наружной обшивки и других конструкций с переменной
толщиной, варьируя число слоев, укладываемых на том или ином участке.
Благодаря этому удается получить прочные и легкие корпуса, жесткость
которых обеспечивается минимальным количеством набора.
Плотность стеклопластика в готовой конструкции
составляет 1,65-1,75 г/см3; временное сопротивление разрыву -
2500 - 3000 кгс/см2; допускаемое напряжение на изгиб - 750 - 950
кгс/см2.
Стеклопластик можно резать ножовками по металлу,
алмазными отрезными кругами (при использовании электродрели или
специальных пневматических машинок), опиливать напильниками, сверлить
и нарезать в нем резьбу. Стеклопластик - материал абразивный,
поэтому режущий инструмент необходимо применять из твердых сплавов;
надо правильно затачивать его на тяжелый режим работы. Грубое
опиливание пластика можно выполнять рашпилем и драчевыми напильниками,
чистовое-личными напильниками с рабочими поверхностями натертыми
мелом. Это уменьшает забивание напильника опилками и повышает
его стойкость.
Конструкции из стеклопластика соединяют при помощи
склеивания, приформовки, болтовых соединений и комбинация этих
способов.
Приформовка деталей осуществляется последовательным
наложением полос стеклоткани на связующем, с применением которого
были изготовлены эти детали (рис. 60). Поверхности деталей в местах
приформовки предварительно зачищают шкуровальным кругом с мелкой
зернистостью. Зазоры между деталями заполняют смесью, состоящей
из 50 % рубленого стекловолокна и 50 % (по массе) связующего.
Стеклоткань для угольников и накладок раскраивают таким образом,
чтобы каждый последующий слой перекрывал по ширине предыдущий;
при большой толщине приформовки делать более двух полос одинаковой
ширины не рекомендуется.
Непосредственно перед приформовкой поверхности деталей,
на которые будет накладываться стеклоткань, обезжиривают ацетоном,
тщательно протирают сухой ветошью и выдерживают 20 мин. для испарения
ацетона. Затем укладывают самую узкую полосу, тщательно пропитывая
ее связующим и разглаживая, чтобы удалить попасшие под нее воздушные
пузыри. Затем укладывают последующие слои. Последний слой должен
перекрыть все предыдущие и свести образовавшееся утолщение "на
нет", что обеспечивает отсутствие концентрации напряжений в местах
резкого изменения толщины.
Толщина полки приформовочного угольника обычно
принимается равной половине толщины присоединяемой детали, ширина
- 7-8 толщинам полки угольника (около 50 мм на малых лодках и
яхтах).
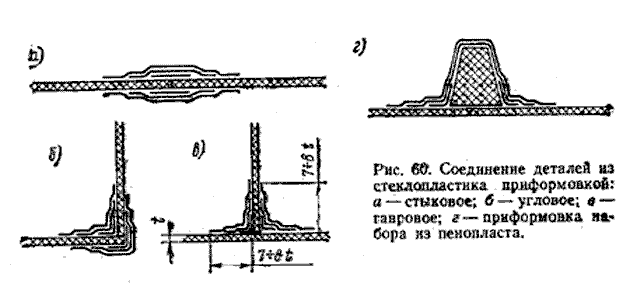
При выполнении приформовок не рекомендуется применять
больших усилий для подтягивания деталей друг к другу или запрессовки
соединяемых элементов -это может привести к выдавливанию связующего.
Помимо изготовления корпусов и их оклейки стеклоткань
и связующее могут применяться для соединения корпусных деталей
из фанеры и пенопласта. В частности получила распространение технология
постройки небольших фанерных судов на проволочных скрепках
с последующей оклейкой полосами стеклоткани на связующем. Сущность
метода ясна из рис. 61. Скрепки делаются из медной проволоки диаметром
около 2 мм. Их заготовляют, нарезав куски проволоки длиной по
40 мм и изогнув в виде глубоких скобок. Вдоль соединяемых кромок
фанеры через 75 мм просверливают отверстия для концов этих скрепок,
которые вставляют в отверстия с внутренней стороны обшивки и снаружи
туго скручивают при помощи плоскогубцев.
Скрепки являются скорее монтажными элементами, чем
скреплением листов обшивки на все время последующей эксплуатации
лодки. Основную прочность соединению придаст стеклопластик, который
образуется при помощи лент (или полос) тонкой стеклоткани, наклеиваемых
эпоксидным связующим в несколько слоев с обеих сторон соединения.
Чтобы получился плотный слой стеклопластика - без воздушных пузырей
и отслаивания от фанеры, необходимо тщательно утопить в древесину
проволоку, которая выступает изнутри в виде "мостиков" над пазом.
Сделать это можно при помощи молотка и зубила со скругленной рубящей
частью либо другого похожего инструмента; при этом шов получает
дополнительное уплотнение.
Проклеивание соединений начинают с внутренней их
стороны. Перед приклеиванием первой полосы стеклоткани рекомендуется
ограничить ширину намазываемого участка фанеры, наложив на это
место по обеим сторонам паза липкую ленту. Затем на участок между
лентами наносится связующее и накладывается сухая полоса стеклоткани.
При этом полосу просто раскатывают, но не натягивают. Снаружи
стеклоткань простукивают кистью, смоченной в связующем, до равномерной
пропитки ткани, которая при этом становится прозрачной. Воздушные
пузырьки совершенно необходимо тщательно удалять, иначе впоследствии
они послужат причиной расслоения пластика и фильтрации воды. Важно
также плотно прикатать к фанере кромки стеклоленты, чтобы между
деревом и пластиком не образовалась щель.
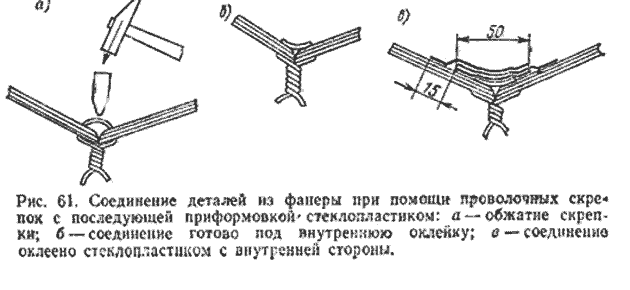
Желательно использовать ленту фабричного изготовления.
В зависимости от толщины соединяемых листов фанеры необходимо
уложить от трех до шести слоев стеклоткани с каждой стороны стыка.
Каждый последующий слой необходимо смещать в ту или иную сторону
от линии стыка с тем, чтобы кромка верхнего слоя перекрывала одну
из кромок предыдущего на 10-15 мм. Если ленты приходится нарезать
из стеклоткани самому, верхние слои можно заранее делать пошире.
Концы отдельных кусков ленты также должны перекрывать друг друга.
Перед оклеиванием стыков или пазов снаружи выступающие
скрутки проволочных скрепок откусывают кусачками как можно ближе
к поверхности фанеры, а оставшиеся кончики проволоки запиливают
напильником вровень с ней.
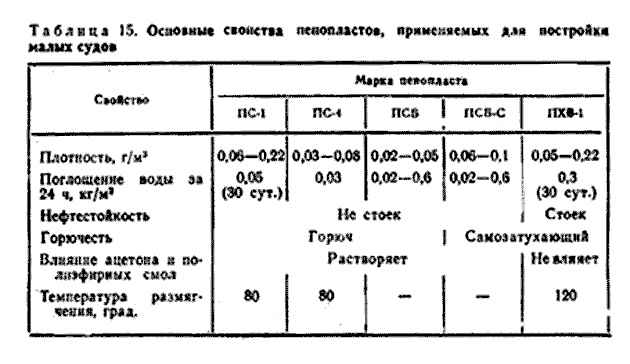
Затем вдоль паза накладывают ограничительные липкие
ленты и наклеивают соответствующее число слоев стеклоткани.
Подобный же метод может быть использован и для тавровых
соединений различных продольных и поперечных переборок с наружной
обшивкой. Для получения достаточной прочности ширина приформовки
должна быть от 25 до 50 мм на каждую соединяемую деталь. Слабыми
местами приформовок являются зазоры между пластиком и деревом
либо пенопластом. При "работе" узла эти зазоры имеют тенденцию
увеличиваться, а попадающая туда влага со временем нарушает прочность
склейки. Поэтому при изготовлении узлов необходимо тщательно прикатывать
кромки полос к соединяемым деталям, а во время эксплуатации судна
своевременно устранять появившиеся зазоры заливкой смолой и дополнительной
оклейкой.
При постройке пластмассовых корпусов широко применяют
различного рода пенопласты. Из них делают оформители балок
продольного и поперечного набора, заполнители отсеков плавучести
и трехслойных-сэндвичевых конструкций (наружной обшивки,
палубы, переборок и т. п.). Основные данные наиболее доступных
пенопластов приведены в табл. 15. Полистироловые ПС-1, ПС-4 и
полихлорвиниловый ПХВ-1 выпускаются в виде плит; пенопласты ПСБ
и ПСБ-С получаются из полуфабрикатов-порошков, вспениваемых в
формах для блоков. Пенопласты легко обрабатываются резанием, склеиваются
между собой и со стеклопластиком эпоксидными клеями и клеем ВИАМ
Б-3 при умеренном удельном давлении запрессовки 0,5-3 кгс/см2.
Расход клея при склеивании пенопластов между собой составляет
от 150 до 400 г/м2; при склеивании с пластиком-около 200 г/м2.
Время выдержки под давлением при использовании клея ВИАМ Б-3 составляет
3-5 ч; эпоксидного компаунда К-153-10-24 ч. Изделия, склеенные
без подогрева (при температуре 16-25 °С), можно обрабатывать по
прошествии 20-40 ч.
Следует учесть, что полистироловые пенопласты ПС-1,
ПС-4 и ПСБ растворяются ацетоном, бензином и стиролом, содержащимся
в полиэфирных смолах. Поэтому использовать смолы марок ПН для
склеивания пенопластов нельзя, так же как и оклеивать пенопластовые
оформители набора стеклотканями на этих смолах. Поверхности пенопласта,
подлежащие оклейке, предварительно должны быть покрыты слоем эпоксидного
связующего или клея ВИАМ Б-3.
Для силовых деталей набора лучше применять более
тяжелый и плотный пенопласт типа ПХВ-1; в качестве заполнителей
отсеков плавучести хороши ПСБ и ПС-4.
Работая со стеклопластиком, необходимо помнить,
что в состав связующего входят химические вещества, обладающие
токсическими (ядовитыми) свойствами. При определенных концентрациях
их паров в помещении или непосредственном воздействии на кожу
эти вещества могут вызвать заболевание дыхательных путей, кожи
и слизистых оболочек. Поэтому работы по формованию корпусов или
оклейке нужно выполнять на открытом воздухе либо в хорошо вентилируемом
помещении. Формовку нужно производить в резиновых перчатках, тщательно
мыть руки теплой водой с мылом в случае попадания на них связующего.
Защитить кожу рук от действия смолы можно применением защитных
мазей- Селисского, "биологических перчаток". По окончании работы
и мытья рук рекомендуется их смазать вазелином, ланолином или
подобными жирными мазями.
Работая со стеклотканью, нужно надевать защитные
очки, чтобы в глаза не попадали частицы стекловолокна, а на лицо-марлевую
повязку или респиратор для защиты органов дыхания.
§ 5. Металлы
В последние годы число людей, знакомых с обработкой
металла лучше, чем со столярным искусством, заметно увеличивается.
Неудивительно, что довольно часто судостроители-любители избирают
для постройки своих судов сталь или же легкие сплавы, несмотря
на сложность приобретения этих материалов. Нередко для этой цели
используют старые металлические конструкции, подлежащие переплавке,
из которых удаётся вырезать вполне кондиционные листы для наружной
обшивки лодки. Кроме того, металл оказывается наиболее подходящим
материалом для заводских и студенческих коллективов, строящих
суда коллективного пользования.
Стальные корпуса строят из обычной углеродистой
стали марки Ст. 3 или из стали повышенного качества марки Ст.
15. Толщина наружной обшивки составляет от 1,5-2 мм на лодке длиной
6 м, до 3 мм на катере длиной более 10 м. Набор корпуса делается
из полос, полособульбовых и угловых профилей соответствующих размеров.
Наиболее простой и дешевый способ соединений деталей
стальных корпусов - сварка. Однако даже опытные сварщики
не могут обеспечить качественный шов при толщине металла 1-1,2
мм. Так как обшивку при сварке сильно коробит, то приходится брать
листы большей толщины (1,8-2 мм), что значительно утяжеляет корпус
небольшого катера или яхты.
При клепаной конструкции толщину листов
можно выбрать минимальную (0,8-1 мм), но труда придется затратить
значительно больше, чем при изготовлении сварного корпуса.
Стальные корпуса, построенные любителями, не только
тяжелее корпусов, аналогичных по размерам и выполненных из древесины,
легких сплавов или пластмасс, но и обходятся гораздо дороже. Кроме
того, для изготовления стальных корпусов требуются сварочное оборудование
и специальные приспособления.
Легкие сплавы часто используются любителями
для постройки легких глиссирующих лодок и катеров. Корпуса получаются
легче, чем из дерева.
Наиболее прочны сплавы алюминия с медью типа
дюралюминия. Обшивка выполняется из листов толщиной от 0,8
мм (на лодках длиной 3-4 м) до 2,5 мм (на катере длиной до 10
м). Дюралюминий марки Д15-термически упрочняемый сплав, листы
его подвергаются закалке. Для изгиба по малому радиусу (например,
для отгиба фланцев) деталь нужно отпустить, предварительно нагрев
ее до 350 °С и остудив на воздухе, иначе в материале появятся
трещины. После обработки деталь можно снова закалить нагревом
до 500 0С и охлаждением в воде. Из дюралюминия строятся корпуса
только клепаной конструкции.
Существенным недостатком дюраля является его сравнительно
низкая коррозионная стойкость, особенно в морской воде. Причиной
тому являются образующиеся в воде электролитические микропары
алюминий - медь. Обычно листы металла, выходящие с прокатного
завода, покрывают тонким слоем чистого алюминия (так называемым
плакирующим слоем) для защиты дюралюминия от коррозии в процессе
производства и хранения металла. Готовые корпуса из дюралюминия
нуждаются в тщательном лакокрасочном покрытии.
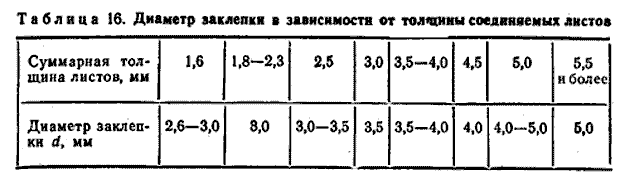
Алюминиево - магниевые сплавы типа АМг обладают
лучшей стойкостью против коррозии, чем дюралюминий; корпуса из
них могут эксплуатироваться в морской воде. Эти сплавы пластичны,
листы и профили из них могут подвергаться гибке в холодном состоянии,
хорошо свариваются аргоно-дуговой сваркой. Обшивку приходится
применять большей толщины, чем из дюралюминия, так как сплавы
АМг менее прочны. Если даже обшивка лодки и не получит течь, после
ударов о волну или причал на ней могут появиться вмятины между
шпангоутами, ухудшающие внешний вид и ходовые качества. В случае
применения сварки очень трудно избежать коробления тонкой обшивки
при ее соединение с набором: по сравнению со сталью, алюминий
обладает в 2 раза более высоким коэффициентом линейного удлинения
при нагреве, поэтому и деформации при сварке соответственно больше.
Все это заставляет использовать для наружной обшивки листы толщиной
не менее 2 мм, а при постройке корпусов длиной более 5 м - уже
толщиной 3-4 мм.
Клепаные соединения. Для клепаных соединений
дюралевых корпусов применяются анодированные заклепки из сплава
Д18П и В65; для корпусов из алюминиево-магниевых сплавов-из АМг5П.
Швы, крепящие угольники набора к обшивке, выполняют однорядными
с шагом от 8 до 10d-диаметров заклепки. Водонепроницаемые прочно-плотные
швы выполняются двухрядными (заклепки располагаются в шахматном
порядке) с шагом в каждом ряду от 3 до 5 d. Расстояние между рядами
заклепок, обуславливающее прочность и плотность соединения, принимается
разным, в зависимости от типа соединения (2-5)d; например, для
соединений листов обшивки расстояние между рядами должно быть
3d. Отстояние от центра заклепки до кромки листа или профиля принимается
равным 1,8 - 2d.
Детали можно соединять внакрой либо встык на односторонних
или на двусторонних планках-подкладках.
Диаметр заклепок d может быть принят равным удвоенной
толщине материала, из которого изготовлены соединяемые детали,
а при разных толщинах соединяемых листов можно пользоваться данными
табл. 16 в зависимости от суммарной толщины склепываемого пакета.
Длина стержня заклепки должна равняться общей толщине
склепываемых листов, сложенной с величиной Р, необходимой для
образования замыкающей головки; для полукруглой головки Р = l,5d;
конической-1,3й d ; полупотайной- l,ld; потайной-0,9d. Заклепки
с полукруглой, конической или бочкообразной закладной головкой
применяют для клепки соединений набора. Днищевую обшивку в кормовой
части глиссирующих лодок для уменьшения сопротивления воды целесообразно
клепать заклепками с потайными закладными головками (если, конечно,
толщина листа позволяет сделать зенковку). Остальную часть обшивки
днища, борта и палубу можно клепать заклепками с плоско-выпуклыми
полупотайными головками.
Отверстия под клепку делают сверлом, имеющим диаметр
на 0,1 мм больше диаметра заклепки.
Гнезда под закладные головки потайных и полупотайных
заклепок зенкуют на угол 90°. Глубина гнезд для потайной закладной
головки при обратном способе клепки должна быть на 0,1 мм меньше
высоты головки заклепки, а при прямом способе - равна высоте головки.
При прямом способе клепки удары молотком наносят со стороны замыкающей,
т. е. расклепываемой головки, при обратном - со стороны закладной
головки. Обратный способ применяют тогда, когда, например, неудобно
наносить удары изнутри корпуса (как правило, заклепки закладывают
снаружи). Если закладная головка не плоская, то удары по ней наносят
через обжимку с лункой по форме головки. Формируемая головка образуется
за счет расплющивания конца стержня заклепки на массивной поддержке.
Перед клепкой детали собирают на монтажные (сборочные)
болты, устанавливаемые через каждые 10-12 отверстий. Клепку ведут
от середины шва к краям; под конец сборочные болты снимают, заменяя
их заклепками.
Процесс клепки прямым способом выполняется так:
под закладную головку заклепки, введенной в отверстие, устанавливают
поддержку; на стержень заклепки надевают обсадку, уплотняют соединение
несколькими ударами молотка, после чего формируют замыкающую головку,
ударяя молотком по выступающему из соединения стержню заклепки.
При необходимости замыкающую головку, формируют обжимкой.
|