Джеймс Гиллиам
Перевод mailto:boris@itam.nsc.ru">Бориса Постникова
Источник: сайт http://boatdesign.net">"boatdesign.net"
Дизайн, конструкция и материалы мачт, такелажа и парусов претерпели значительные
изменения на протяжении 20 века: от цельнодеревянных мачт, сделанных из одного дерева,
до аэродинамически выверенных, сверхлегких и сверхпрочных карбоновых профилей. Паруса
прошли путь от натуральных материалов, таких как хлопок, который имел тенденцию разлагаться
и растягиваться, до новых материалов вроде "North sails 3DL", где применены
вектран, углеволокно, кевлар, необычные покрытия и клеи. Мы рассмотрим историю этих
изменений и технологические достижения, обусловившие их.
Введение.
Парусное вооружение является "электростанцией" парусной лодки. Через развитие новых материалов
для вооружения может быть повышена его техническая эффективность и надежность. Это позволяет
яхтам стать быстрее. Во второй половине 19 века гонки на яхтах стали спортом. Изначально
появились гонки, такие как Кубок Америки, которые привели к развитию правил обмера и гандикапа.
Так началось развитие гоночных лодок с целью раздвинуть границы этих правил. Значительные
достижения в характеристиках могли бы быть получены через усовершенствование вооружения.
С началом нашего столетия произошел ряд изменений в материалах и производстве: от использования
хлопчатобумажных парусов и деревянного рангоута на смене 19 столетия до карбонового рангоута
и парусов из кубенового волокна, нашедшие свое место на борту нового поколения яхт.
Перед тем как рассмотреть достижения в технологии парусного вооружения, необходимо понять,
каковы цели улучшений.
Они включают в себя:
- Надежность
- Вес (чем легче, тем лучше)
- Цена
- Регулируемость
- Сопротивление разрушению окружающей средой
- Эффективность
Цель дизайнера и производителя заключается в поиске компромисса всех вышеперечисленных
требований с возможностями технологии и материалов.
Обычно новые технологии и материалы сначала появляются на развивающихся классах, таких
как международный класс "14-футов" (14's) и "Мос" (Moth). Эти технологии
со временем переходят и в другие классы. Новые достижения традиционно развиваются и проверяются
первоначально на яхтах, состязающихся на вершине спортивного Олимпа. Наиболее дорогие
и радикальные усовершенствования происходят с яхтами, участвующими в Кубке Америки. Кубок,
с самого начала своего возникновения в 1851 году, был источником большинства новых технических
достижений. Технические усовершенствования медленно приживаются на классах монотипах,
поскольку они призваны быть однотипны, недороги при покупки и содержании, что в основном
определяет выбор материалов и конструкции вооружения.
Материалы для мачт и их производство.
Развитие мачт:
Было три основных изменения в материалах для мачт, происходившие в следующем порядке:
дерево, алюминий, композиционные материалы. Хотя в настоящее время все эти материалы пока
применяются в яхтах и динги, но для высококлассных гоночных машин применяется только кубеновое
волокно.
Деревянные мачты:
Дерево было наиболее распространенным материалом для мачт в начале 20 века. У него есть
несколько основных недостатков:
- Это не легкий материал, особенно в сравнении с современными композитными мачтами
- Наибольшая прочность достигается применением цельной древесины
- Подвержено гниению, если специально не обработано.
Проблема большой прочности цельной древесины стала важной для Британии в начале века.
Во время промышленной революции обширные площади лесных угодий были ликвидированы по различным
причинам: постройка кораблей и на дрова. Это означало, что требуемый для изготовления
мачт лес, стало труднее добывать, и поэтому он стал дороже при поставке.
Деревянные мачты использовались много тысяч лет и показали себя как надежные средства
несения парусов. Все изменилось в 20 веке, как только лодки стали строить исключительно
для скорости и гонок. Затраты на труд и материалы при производстве деревянных мачт потеряли
экономический аспект по сравнению с конечным результатом.
Алюминиевые мачты:
Впервые алюминиевые мачты появились на динги после Второй мировой войны. Они были опробованы
на развивающихся международных классах динги, таких как "Мос" и "14's".
На этих классах были испытаны относительно недорогие при поставке стандартные алюминиевые
профили, используемые в аэрокосмической промышленности.
В настоящее время алюминиевые мачты используются на большинстве прогулочных и на большом
количестве гоночных классов. Алюминий применялся в 30-х годах на больших классах, таких
как яхта J-класса "Шэмрок V" (Shamrock V).
Размер мачты, которую необходимо сконструировать, в основном определит и применяемый метод
производства. При производстве мачт для простых динги и легких крейсеров широко применяется
стандартный метод штамповки выдавливанием мачтовой секции, при этом алюминий выдавливается
через шаблон. Затем отрезается мачтовая секция желаемой длины и крепится оснастка. Это
наиболее дешевый способ получения алюминиевой мачты, поскольку не требуется использование
дорогого оборудования и пресс-форм. Методы конструирования и производства, применяемые
при выдавливании алюминиевых мачт, мало изменились с 70-х годов, тем не менее, это самый
популярный сегодня тип мачты. Это же метод может быть использован для больших мачт и мачт
с высокими характеристиками. Единственное отличие заключается в том, что на вершине мачты
делается треугольный паз, кромки которого сгибаются и свариваются. В результате получается
профилированная топовая часть, позволяющая мачте лучше изгибаться.
Последнее развитие алюминиевых мачт связано с алюминиевым сплавом "алюстартм" (Alustartm),
разработанным для судостроения. При 20% увеличении прочности по сравнению с другими корабельными
сортами сплавов при его применении может быть уменьшена толщина листа. Тем самым снижается
вес мачты [1]. "Алюстартм" сохраняет коррозионную стойкость, гибкость и сварные свойства
наравне с другими алюминиевыми сплавами в своей группе. Из этого сплава изготовляются
листы, которые используются при конструировании алюминиевых листовых мачт. Говорят, что
эти мачты прочнее и легче, чем полученные выдавливанием, хотя пока не известно еще ни
одного сравнения.
Мачты из углеволокна:
Мачты из углеволокна начали использоваться с начала 90-х, сначала на яхтах-участницах
Кубка Америки и Адмиральского кубка. Через десятилетие после своего первого применения
углеволокно все еще не столь широко распространено, как можно подумать.
С применением углеволокна мачта может быть сделана более легкой и жесткой, чем алюминиевая.
Это может очень сильно улучшить характеристики вооружения. Существует два основных метода
производства углеволоконных мачт. Первый состоит в том, что используется стандартная профильная
форма для производства равномерного по длине профиля мачты. Это наиболее дешевый тип углеволоконных
матч, так как формы для производства стандартного профиля могут быть использованы многократно.
Они также могут быть изготовлены для однократного применения для какой-нибудь определенной
яхты. Этот тип мачт более дорогой, поскольку форма должна быть сделана под определенные
технические требования, и обычно используется один раз. Основная проблема углеволокна
заключена в дополнительной стоимости материалов и увеличенных трудовых затратах. Типичная
углеволоконная мачта будет в 7 раз дороже алюминиевой.
С использованием современных компьютерных технологий, таких как CFD (численная газовая
динамика) и FFA (конечно-элементный анализ), возможно рассчитать точные нагрузки на мачту.
Поэтому углеволоконная мачта может быть изготовлена с повышенной прочностью в направлениях
основных нагрузок. Для оптимальной формы паруса очень важна гибкость мачты, она делает
парус более плоским. А поскольку углеволоконная мачта может быть произведена с точно контролируемой
ориентацией волокон, то возможно создать мачту, которая будет иметь известные характеристики
по изгибу. Это важное продвижение технологии в совокупности с успехами в парусной технологии
дает возможность сформировать превосходную аэродинамическую форму, которая вряд ли может
быть достигнута на алюминиевой мачте и полиэстеровых парусах. Также следует учесть, что
использование CFD позволяет определить воздушный поток вблизи мачты, а более мощные программы
рассчитать взаимодействие парусов и стоячего такелажа.
Углеволокно представляет собой материал очень хорошо подходящий для производства мачт.
Это дает высокую прочность вкупе с легким весом. Могут быть изготовлены сложные формы,
которые доказали свою надежность. Однако недавно с углеволоконными мачтами были проблемы.
Развитие углеволоконных мачт для яхт Международного Класса Кубка Америки (IACC yachts)
показало, что, когда углеволоконная мачта повреждается (обычно из-за недоработок при конструировании
или выходе из строя другого рангоута или такелажа; обычно это приводит к поломке мачты),
то образующиеся при этом щепки углеволокна могут нанести ущерб команде или лодке.
Сравнение материалов для мачт:
В мачтах трудно сравнивать за и против, поскольку усилие на мачту зависит в значительной
степени от момента инерции поперечного сечения мачты. Так как при применении каждого из
трех используемых материалов будет различная форма профиля, то сравнивать достаточно трудно.
Другим важным моментом для мачтового материала является величина аэродинамического сопротивления
мачты, которое может быть снижено уменьшением ширины мачты в сочетании с выбором оптимальной
аэродинамической формы. Это легко достигнуть с углеволокном, поскольку прочность мачтового
профиля без проблем проектируется с различными моментами инерции в любом направлении.
Наивысшая прочность и жесткость необходима по боковым направлениям и в меньшей степени
вперед и назад. Это означает, что в случае с деревянной мачтой, необходимо избыточное
количество дерева в переднем и заднем направлении, что в свою очередь приводит к увеличению
веса.
Мачтовые технологии в будущем:
С тех пор как появилось углеволокно, поиск альтернативных материалов для мачт ведется
не активно. Но продолжается конструкторская работа по максимальному использованию возможности
углеволокна.
Дальнейшее развитие мачт может происходить за счет применения новых матричных материалов
и нового волокна. Волокна, такие как PBO (p-phenylene-2,6-benzobisoxazole, прим. Пер.),
могут поднять характеристики мачты. Свойства любого композитного материала могут быть
значительно улучшены применением более совершенных методов производства. Наиболее очевидно
использование автоклава, который позволяет намного лучше скреплять слоистый материал.
В результате получается более прочный и легкий ламинат.
Безтакелажный
рангоут и рангоут - фиксированное крыло:
Безтакелажный рангоут был популярен многие годы. Его наиболее успешные примеры - швертботы
Лазер (Laser) и Топпер (Topper), разработанные в 70-х. Их рангоут очень удобен. Его преимущество
заключается в снижении паразитного сопротивления за счет отсутствия стоячего такелажа.
Аэрориг (Aerorig) является ведущей компанией, производящей данный тип рангоута. Безтакелажный
рангоут в основном ограничивается прогулочными яхтами. Его редко можно встретить на борту
гоночных яхт по ряду причин, самая очевидная из которых - простота, позволяющая не иметь
достаточно хороших яхтенных навыков. Но это, тем не менее, не означает, что такой рангоут
хорошо подходит для прогулочных яхтах. На рис.1 показана яхта с самым большим
на настоящее время безтакелажным рангоутом с высотой мачты 60 м (197 футов). Преимущество
этой яхты в том, что рангоут хорошо сбалансирован и с ним может управляться один человек.
Ключевыми моментами при разработке данного рангоута были технологические достижения в
материалах и новое понимание того, как ведет себя композитный материал под нагрузкой.
Первое заметное упоминание о рангоуте типа фиксированное крыла может быть найдено на желтых
страницах (Yellow Pages), посвященных рекорду скорости на воде.
Материалы для рангоута со стоячим такелажем.
Стоячий такелаж из витых стальных нержавеющих тросов:
Это
наиболее распространенный тип стоячего такелажа, прижившийся на борту яхт и динги. Он
коррозиеустойчив, гибок и недорог. Насколько я знаю, такой такелаж использовался на большинстве
яхт второй половины 20 века, несмотря на то, что успехи в улучшении качества стали и ее
производстве были невелики. Его недостатки в том, что он достаточно тяжел при заданной
прочности и, что важно, до некоторой степени растягивается. Поэтому велись исследования
в направлении поиска более прочного, меньше подверженного растяжению и более однородного
материала. Витой трос имеет многообразие конфигураций. Наиболее популярные виды показаны
на рис.2 и рис.3. Различное расположение отдельных волокон
троса значительно влияет на его свойства. На рис. 5 приведены данные модуля
упругости для двух различных типов проволочного троса.
Стальной
трос 1x19 имеет модуль упругости приблизительно в два раз больше, чем у троса 7x7. Это
показывает влияние конфигурации волокон на изменение характеристик троса.
Были
некоторые разработки, направленные на уменьшение диаметра при заданной прочности витых
тросов. Например, витой трос Диформ (Dyform) (рис.4) имеет пониженное аэродинамическое
сопротивление, схожее с цельным такелажем, и 30% увеличение в прочности на разрыв по сравнению
с традиционным тросом 1x19. На рис. 4, где приведено поперечное сечение,
видно, как специально формованные волокна максимально заполняют сечение троса Диформ [2].
Его более гладкая внешняя поверхность в сравнение с обычным тросом уменьшает паразитное
аэродинамическое сопротивление стоячего такелажа.
Цельный стоячий такелаж:
Трудно определить, когда цельный такелаж стал применяться на яхтах. Я полагаю, что он
появился в 80-х, как альтернатива свитому проволочному такелажу для получения более упругого
рангоута с улучшенными характеристиками. Что и было достигнуто. Струны стали набирать
популярность. В большей степени такой такелаж был на больших прогулочных яхтах, а также
применялся на большинстве лодок со средними и высокими гоночными характеристиками. Существует
целый ряд различных материалов, используемых для струн. Наиболее распространенным, по
всей видимости, является Нитроник 50TM (Nitronic 50TM) - это высококлассная судовая нержавеющая
сталь. Применяются также кобальтовые, карбоновые и кевларовые струны.
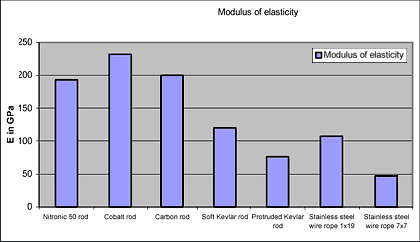
Рис.5: Модуль упругости в ГПа для различных материалов.
Слева направо: струна из нитрона 50, кобальта, карбона, мягкого кевлара, кевлар после
протрузии, стальной нержавеющий трос 1x19, стальной нержавеющий трос 7x7.
Сравнительный анализ различных струн:
Модуль упругости определяется следующей формулой:
S=(PхL) / (AхE),
где S = удлинение нагруженного троса,
P - приложенная нагрузка,
L - длина троса,
A - площадь поперечного сечения,
E - Модуль упругости.
На рис.5 приведена сравнительная жесткость различных типов материалов стоячего
такелажа. Легко видеть, что большинство материалов для струн почти в два раза жестче материалов
проволочных тросов. Мягкая кевларовая струна не имеет выдающихся характеристик в сравнении
с другими струнами и тросами и в основном используется для бакштагов, где основными требованиями
являются высокая прочность и умеренная жесткость.
Основным параметром при выборе стоячего такелажа является прочность на разрыв - максимальная
нагрузка, которую выдерживает трос или струна без разрыва. В целом струна примерно на
20% прочнее троса того же самого диаметра.
Важным параметром является усталость. При условии, что такелаж закреплен таким образом,
что возможны только небольшие отклонения по углу атаки, больших проблем с усталостным
разрушением не будет. Трос более чувствителен к усталости так как образующие его проволоки
трутся друг о друга. Но струна чувствительна к повреждению поверхности, что может привести
к образованию усталостных трещин. Тут трос имеет преимущество. Когда он разрывается от
усталости, его проволоки рвутся одна за другой и поэтому здесь легче найти проблемное
место и отремонтировать. С другой стороны, струна рвется мгновенно и визуальным осмотром
практически невозможно найти следы зарождения трещины.
Удлинение нагруженного троса или струны увеличивается пропорционально нагрузке и длине
и обратно пропорционально площади поперечного сечения и модулю упругости. Удлинение такелажа
имеет огромное влияние на его общую эффективность. Пока нагрузка находится в пределах
70% от предельной нагрузки на разрыв пластической деформации нет. Меньшее удлинение позволяет
сделать более жесткий негибкий такелаж.
В результате лодка меньше лежит на руле (менее склонна к приведению), хотя это обычно
немного и составляет 2-3%. Также, чем меньше мачта заваливается на подветер и меньше сгибается,
тем выше сопротивление изгибу.
Аэродинамическое сопротивление вант и штагов увеличивается с увеличением их диаметра.
Струна той же самой прочности, что и трос имеет меньший диаметр, а также более гладкую
поверхность, тем самым, вызывая меньшее сопротивление.
Парусные материалы и технологии.
Хлопчатобумажные паруса:
Такие паруса были наиболее распространены по всему миру. Это материал дешев и легок в
производстве. Хлопчатобумажное (ХБ) волокно, будучи натуральным, плохо сопротивляется
разложению, ультрафиолету и впитыванию воды. Эти качества сделали ХБ ткань неподходящей
для парусов высококлассных гонок, что направило парусное производство на путь поиска новых
материалов и на развитие новых методов производства, с целью повысить сопротивляемость
ткани механическому повреждению и воздействию окружающей среды.
Ламинированая
и композитная парусина:
Последние достижения заключались в ламинированых парусах, таких как ткань Норс Сэилс 3DL
(North sails 3DL - трехмерный ламинат). Эти ткани имеют волокна, направленные по линии
основных нагрузок, что позволяет парусу быть легче и прочнее, чем традиционные полиэстеровые
или даже обычные ламинированные паруса.
Существует широкий диапазон парусных тканей от ламинированых полиэстеровых парусов для
прогулочных лодок, до ламинированых кубеновых парусов для яхт-участниц Кубка Америки и
других высококлассных лодок (типа 60-футовых яхт гонок Вольво Оушен (Volvo Ocean), а также
60-футовиков открытого класса - (Open 60's)). Чем дороже ткань, тем она прочнее, легче
и лучше сопротивляется растяжению.
Основное преимущество ткани с ламинированием заключается в том, такой парус будет держать
свою форму лучше и дольше, чем просто полиэстеровая ткань.
На рис. 6 видно, каковы основные причины, почему ламинированая парусина
превосходит тканую. На ламинированой ткани фактически нет извитости. Это означает, что
такая парусина прочнее и лучше сопротивляется растяжению.
Рис.7.
Ламинированая парусина. Слои снизу вверх: полиэстеровая таффета, полотно спектра, майларовая
пленка, полиэстеровая таффета.
На рис.7 показано, как устроен ламинат. Основной носитель нагрузки здесь
полотно из спектра (Spectra). Майларовая (Mylar) пленка удерживает волокна спектра и служит
защитным слоем для него. Полиэстеровая таффетовая покрывающая поверхность предназначена
для повышения сопротивления трению и дает общий высокий уровень защиты для ламината. Такой
подход обычно применяется для парусины прогулочных яхт, потому что это более тяжелый и
более надежный ламинат, чем применяемый на гоночных лодках.
Недостаток, который является общим для ламинированой и других тканей, - подверженность
воздействию ультрафиолетовых лучей. Это общее свойство большинства типов тканей. Были
разработаны новые пленки для ламинирования, чтобы противодействовать ультрафиолету, но
ни одна из них пока не может служит надежной защитой от ультрафиолетовых лучей.
Парусная ткань:
В начале 20 века большинство используемых парусных тканей были хлопчатобумажными или льняными.
ХБ, как натуральное волокно, плохо сопротивляется разложению, ультрафиолету и впитыванию
воды. Эти свойства сделали ее неподходящей для парусины.
Нейлон стал первым, созданным человеком волокном для использования в качестве парусная
ткань. Химическая формула и основные свойства нейлона мало изменились за прошедшие годы.
Он дешев, надежен и относительно неплохо сопротивляется ультрафиолету, имеет хорошую изгибо-усталостную
сопротивляемость и средние прочностные свойства. Тем не менее, применение нейлона ограничено
в основном спинакерами, так как он плохо сопротивляется растяжению. Но даже и для спинакеров
он не идеальный материал, поскольку может впитывать до 3% воды от веса самого спинакера.
Важный прорыв произошел в середине 50-х, когда была изобретена полиэстеровая парусина.
До 80-х единственной широко применяемой парусной тканью был тканый полиэстер (или дакрон
(Dacron) - торговая марка полиэстеровой нити фирмы Дюпон (Dupont)). Дакрон представляет
собой отличную парусную ткань - надежную, не абсорбирующую воду, не подверженную воздействию
плесени.
Тканая парусина имеет врожденную проблему с растяжением. Некоторые нити могут быть пропущены
друг под другом. Со временем под нагрузкой нити стараются выпрямится, приводя, таким образом,
к растяжению ткани. Это обычно называют извитостью. Чтобы волокна лежали как можно ровнее,
была разработана ламинированая парусина.
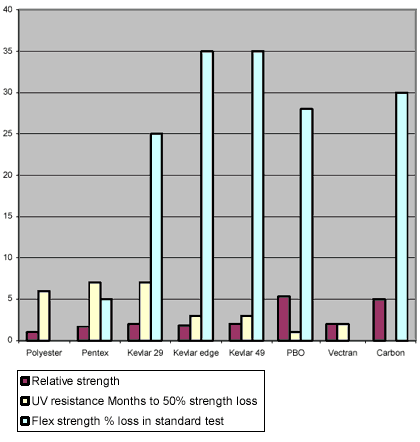
Рис.8. Сравнение парусных тканей: относительная прочность,
сопротивление ультрафиолетовому воздействию в месяцах при 50% потере прочности, прочность
на изгиб, в %, стандартное испытание.
Слева направо: полиэстер, пентекс, кевлар 29, кевлар эдж, кевлар 49, PBO, вектран,
карбон.
Следующим развитием полиэстера, имевшем место в 90-х, стала разработка пентекса (Pentex),
который является производной от полиэстера и имеет модуль упругости в 2,5 раза больше
традиционного полиэстера. Это позволяет парусу больше сопротивляться растяжению и дольше
держать свою форму.
В середине 80-х парусные производители начали развитие ламинированых парусов. Они должны
были быть разработаны для яхт Кубка Америки и высококлассных гонок. В результате получился
ламинат - более легкий, прочный и с более высоким сопротивлением растяжению.
Сравнение современных парусных тканей приведено на рис.8 и 9:
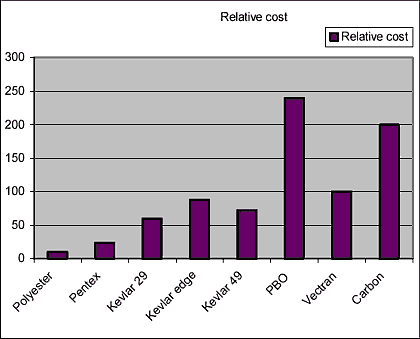
Рис.9. Относительная стоимость по данным [3]. Слева направо: полиэстер, пентекс,
кевлар 29, кевлар едж, кевлар 49, PBO, вектран, карбон.
index.php?pirs=stories&st=istoria_rig_sail1">Продолжение статьи >>
|